GE partners with Virginia Tech engineers to improve wind energy efficiency
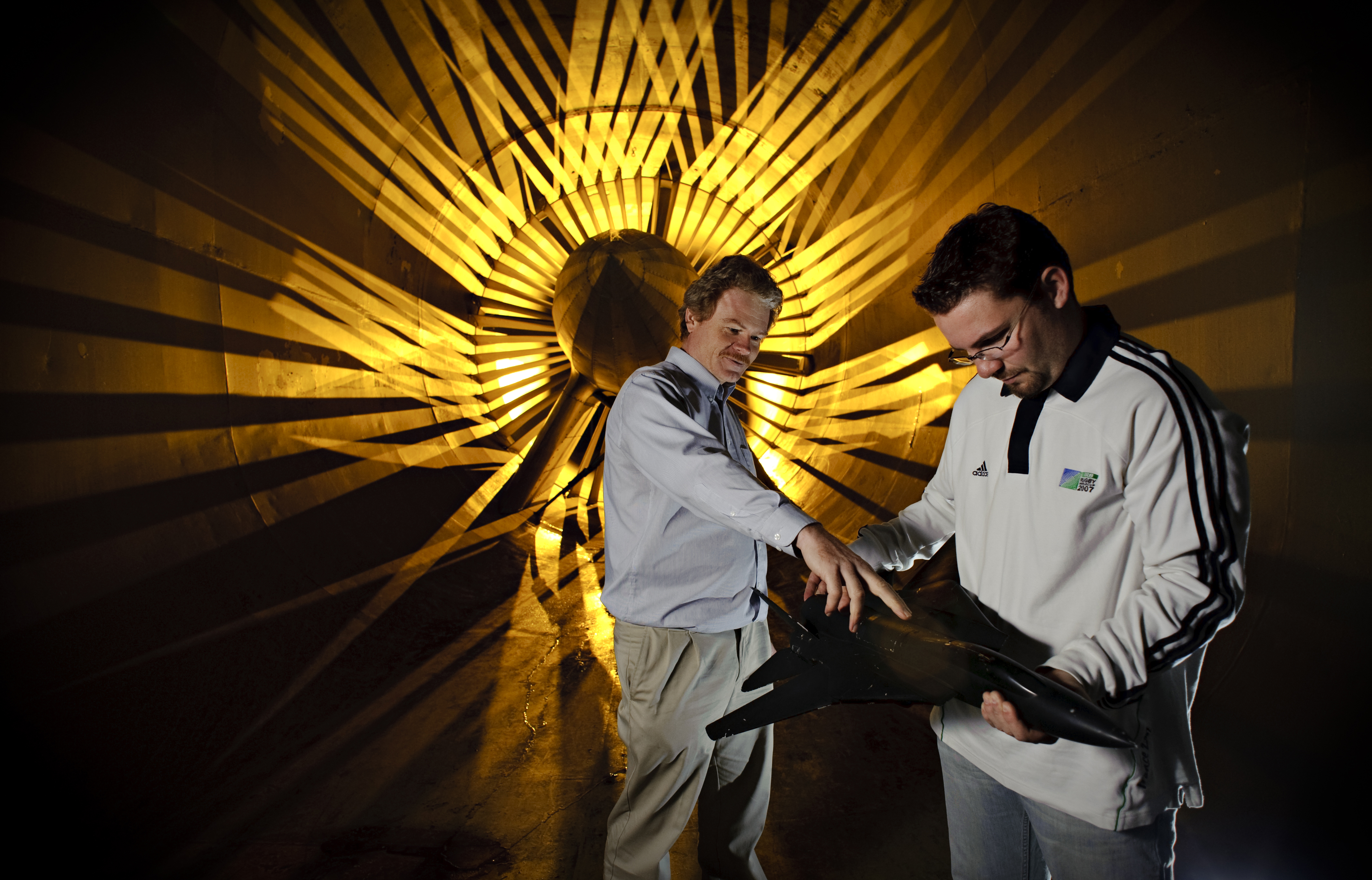
A new method of manufacturing wind turbine blades, used in the capturing of energy that produces power, is expected to enable the construction of much larger wind turbines with higher efficiency and lower costs.
The Advanced Research Project Agency -- Energy, an agency within the U.S. Department of Energy, is funding the $3.7 million project proposed by GE that has partnered with the National Renewable Energy Laboratory (NREL), along with Virginia Tech's William Devenport, professor of aerospace and ocean engineering, and Aurelien Borgoltz, research scientist.
The goal is to develop wind turbine blades using fabric stretched across a frame, instead of today's rigid fiberglass blades. These blades can be manufactured in sections and assembled on site, enabling their construction at costs that are less than currently available.
The cost reduction "represents a significant step toward making onshore wind energy production even more economical as other forms of fossil fuel based energy production without any subsidies," they wrote in their proposal to the DOE.
This new manufacturing method addresses challenges with the current state-of-the-art technology that is looking to produce longer blades, often exceeding 120 meters, in order to increase power output. In the current utility wind energy market, the majority of the wind turbines have rotor diameters of 50 to 100 meters. The concerns are the challenges that the designers face in the production of these longer blades, including transportation requirements, stiffness of material, and equipment needs.
The use of wind blades would need to grow by some 50 percent to achieve a national goal of having the U.S. rely on wind power for 20 percent of its energy needs.
Virginia Tech's role in the three-year research project is to use its wind tunnel expertise to test the aerodynamics and aeroacoustics of this new blade technology. Devenport is the director of Virginia Tech's Stability Wind Tunnel, and Borgoltz is the assistant director.
This facility is one of the largest university operated wind tunnels in the U.S., and by aerospace standards its air flow quality makes it a prime research facility. In recent years it has become world renowned for aeroacoustic testing because of a uniquely advantageous test section arrangement, developed at Virginia Tech. The facility has also become an international leader in wind turbine blade section testing.