One of a kind: Glassblower's work keeps research moving
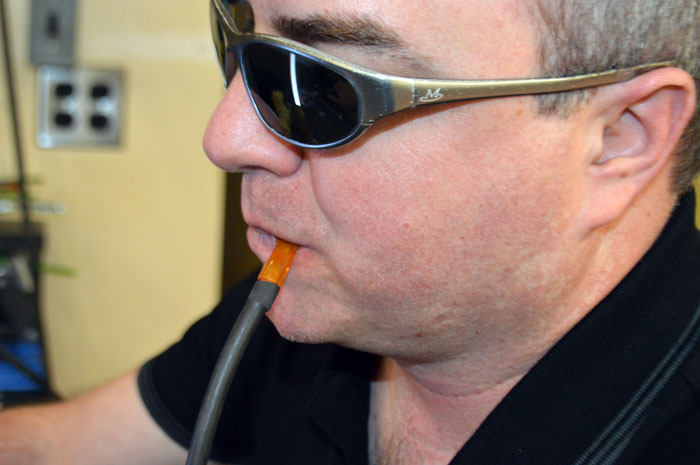
When scientists, engineers, and other researchers at Virginia Tech need a glass component for lab work, they have two options: if it exists, try to order it, or call Tom Wertalik, the university’s only scientific glassblower.
In his Hahn Hall South lab, as a member of the Department of Chemistry, Wertalik puts nearly three decades of glass making experience to use helping researchers invent the future with the help of one very unscientific, primary tool – a flame.
“What I do is technically called lamp working, or flame working, which is a discipline of glass blowing,” Wertalik explained. “The kind you see with the really long pipe, that isn’t what I do.”
And it’s a good thing too, because what people think of as traditional glass blowing is only useful for basic shapes. Wertalik’s work is far more complex.
“People will come in and ask for all kinds of things – many of which don’t exist,” he said. “They’ll bring sketches on pieces of paper or we’ll talk about what they’re trying to achieve and usually we can work something out but not every idea can be made of glass.
“This isn’t a machine shop,” Wertalik explained. “Glass is blown, it’s formed, it’s shaped with hand tools. You can’t get down to extreme tolerances and there will always be variations. My goal is that if I make six of something they should all look similar visually, but they won’t be exact.”
Those items that can be made from glass, however, like a feeding tube for bed-bug research that Wertalik completed for researchers in the Department of Entomology in the College of Agriculture and Life Sciences, are sometimes refinement efforts of existing products. “They brought a couple older versions of some glassware and we made some modifications,” Wertalik said. “It turned out really well, but sometimes it requires a little trial and error like any research. But part of the job is interpreting what the customer is looking for and sometimes you sit down and draw it out until you come up with the right idea.”
The bed-bug feeder is a fairly small, complex piece of glass but some of Wertalik’s larger works can contain more than 20 separate pieces of glass and involve multiple sessions at the torch.
“It’s rare you do a piece that’s finished in a single sitting,” he said. Scientific glass often features multiple glass-in-glass formations that can’t be done at one time but are completed in a series of steps.
“The benefit of scientific glass like this is that it’s relatively inert to most chemicals,” he said. “It takes heat pretty well and won’t expand and crack if you put it over a moderate heat source, which is important for laboratory glassware.”
In addition to the ‘regular’ scientific glass, Wertalik also works with quartz which is even more inert to different chemicals and acids, and has an even higher melting temperature. The quartz he uses doesn’t heat to a flaming orange like most glass. It turns bright white and a solid bar of quartz, when heated, will distribute light out the non-heated end like a flashlight.
“This is the basis for fiber-optics,” he said. “Quartz isn’t used too much in chemistry, but it’s very popular for electrical engineering purposes.”
Although he works in the College of Science, Wertalik does a good deal of work for both electrical and chemical engineering as well. “I’ll do whatever anyone in the university needs,” he said. “I’ve done work for the mining program, environmental departments, whoever -- that’s what I’m here for.”
Wertalik’s ‘being there’ attitude and willingness to sit down and work with clients from anywhere within the university isn’t lost on his customers. “We are the envy of many universities, having a master glassblower like Tom here,” said James Tanko, Department of Chemistry chair. “From the standpoint of the fabrication of scientific glassware, having Tom here means the practical limitation is our imagination. If we can think of it, chances are he can make it.”
The flexibility that Wertalik brings to the university encompasses both cost and time – both important components in research science.
“Stuff that would cost a fortune from an external vendor we can do in house for little more than the cost of material,” Tanko explained. “It’s a major asset to move research forward.”
In-house production can also expedite research, especially in the case of complex or new glassware. When a researcher brings an idea to Wertalik the end product is realized fairly quickly and far less expensively. But the payoff compounds if the researcher realizes the piece doesn’t quite work or if the experiment requires changes to the glassware. In those cases, modifications have to be made, and because it was designed and built in-house, those modifications save a lot more money and time – getting researchers back on track to teach, learn, explore, and discover.
All that science and knowledge realized because of one man, and a flame.