Researchers use local species to expand market for cross-laminated timber
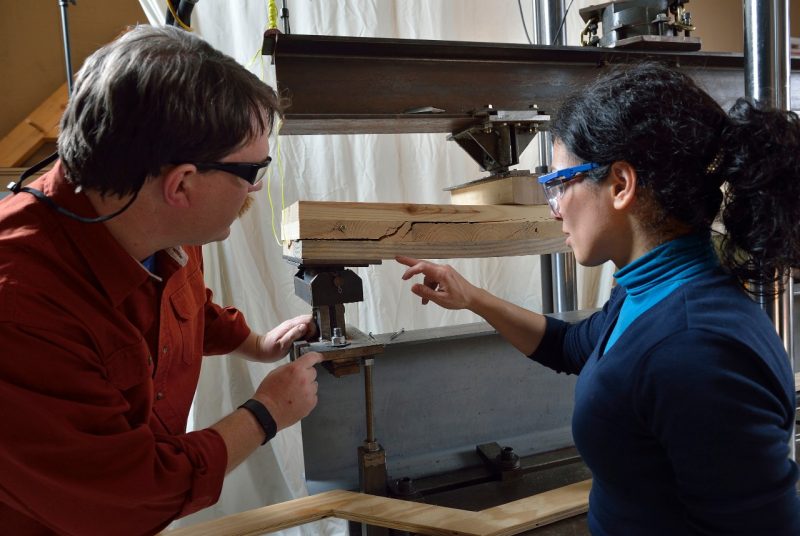
Daniel Hindman, associate professor of wood engineering in Virginia Tech’s College of Natural Resources and Environment, has researched high-performance wood composites for the better part of a decade. Four years ago, he seized the chance to help develop a material made from North American lumber that would be strong enough to replace concrete.
The product is called cross-laminated timber (CLT): solid wood panels up to a foot and a half thick glued together from planks, like massive blocks of plywood. In 2012, he and a team from the college’s Department of Sustainable Biomaterials were awarded a grant to evaluate CLTs made from species native to Virginia.
“The panels themselves are wood and glue, things we’ve had for a century,” Hindman said. “The innovation is in the concept, in thinking about the problem differently: how can we make a large-scale panel out of wood?”
To produce a CLT panel, pieces of lumber are placed side by side and glued together along the edges. The resulting sheets are then stacked with the grain perpendicular to the planks above and below, spread with polyurethane or phenol formaldehyde — the same weatherproof, low-emitting adhesives used in plywood — and sandwiched together in a giant press. The panels can measure up to 10 feet wide, 50 feet long, and from four to 20 inches thick, depending on the number of layers.
The panels’ thickness and alternating grain pattern make buildings constructed with CLTs much stronger than traditional wood-frame structures, in which two-by-fours form a skeleton of studs and joists covered with plywood. A 10-story apartment building was built from CLTs in Melbourne, Australia, in 2012, and an architect in Vancouver, British Columbia, has proposed a 30-story CLT skyscraper.
Designed to handle vertical and lateral loads, CLTs can be made to be stiffer and more stable than conventional wall systems. CLTs behave more like precast concrete: A single panel can form an entire section of wall, floor, roof, or even an elevator shaft without the need for additional structural support.
Along with fellow faculty members Earl Kline, Joseph Loferski, Brian Bond, and Henry Quesada-Pineda, Hindman has designed CLTs from yellow poplar. In addition, Hindman has been working with the Southern Virginia Higher Education Center in South Boston, Virginia, to study the use of southern pine CLTs.
To measure CLT strength, samples were subjected to the department’s universal testing machine — a computerized hydraulic ram — which applies pressure to the timbers until the beams fail. “You know when they’ve broken, because you hear a crack throughout the building,” laughed Department Head Robert Smith.
The southern pine CLT beams split under 15,000 to 20,000 pounds of force, but the yellow poplar surprised Hindman by withstanding up to 35,000 pounds.
For eight- to 15-story buildings, Hindman predicts CLT construction in the U.S. will eventually cost less than steel and concrete. Panels are made to order for each project, and installation is highly efficient. Working from digitized blueprints, mill workers cut openings for doors, windows, light switches, and outlets with a computer-controlled router. At the job site, panels are lifted into place by a crane, and carpenters screw them together.
A small team can finish a structure in a fraction of the time required for other construction methods. A four-man crew assembled the Stadthaus, a nine-floor residential tower in London, in 27 working days, and a 78-foot bell tower in North Carolina was built out of CLTs in just four days.
In addition to wood’s environmental benefits — this renewable resource has half the carbon footprint of concrete — CLT construction requires less energy and generates almost no onsite waste. CLTs weigh up to six times less than concrete, which reduces foundation costs.
In the team’s tests, CLTs matched concrete’s performance in soundproofing and, perhaps surprisingly, fire resistance. “In a catastrophic fire, steel loses its tensile strength and collapses, and concrete cracks up, but wood beams this large will smolder and put themselves out,” Smith said.
First developed in Austria and Germany, CLTs have been popular in Europe for two decades, but American builders have been slow to adopt the technology. Only two plants in the United States produce CLTs approved for structural applications; both firms’ products were certified by the Engineered Wood Association in just the past year. Previously, Americans who wanted to build with CLTs had no choice but to ship the huge panels from Canada or from across the Atlantic.
Hindman and Smith hope a plant will eventually open in Southwest Virginia, but until demand grows, American investors hesitate to gamble on commercial factories. Architects and engineers are trained to use steel and concrete in taller structures, and because CLTs are so new, there isn’t much test data yet on panels made from American wood. Hindman is working to fill those gaps.
“We have to prove CLTs will work before anybody will invest in a plant,” Smith said. “Dr. Hindman’s research is helping us solve these issues.”
Hindman is also researching with manufacturing variables, including the optimal amount of time in the hot press and the best treatments for adhesives, to help potential plant owners perfect their process quickly.
“Only a couple places in the U.S. are doing this type of research,” Smith said. “It’s a great opportunity for us.”