High-performance piezoelectric material could make smart sensors more sensitive
Lab portrait of mechanical engineering professor Shashank Priya
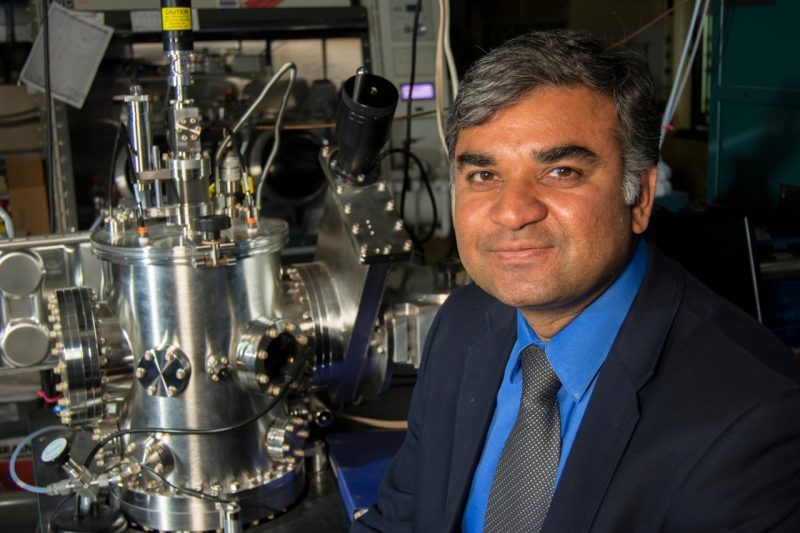
As gathering and transmitting detailed information about the environment becomes an integrated feature of mobile devices, cars, and homes, the race is on among materials scientists to create more sensitive materials for finely tuned sensors.
“The tiniest amount of stress you can detect determines how competitive you are with other sensing technologies,” said Shashank Priya, the Robert E. Hord Jr. Professor of Mechanical Engineering in the College of Engineering and the associate director for research and scholarship at the Institute for Critical Technology and Applied Science.
In a study recently published in Nature Communications, Priya and research assistant professor Yongke Yan report a new composition and synthesis technique for piezoelectric materials that, by controlling the material’s microstructure, increases its sensitivity by three to five times. The technique, developed in collaboration with researchers at Michigan Tech, could enable high-performance sensors for a wide range of applications.
Piezoelectric materials can make ideal sensors because they turn mechanical input, such as sound or pressure changes, into electricity.
“In a smart home, automotive, or industrial environment, for example, you want to measure everything: temperature, pressure, strain, fluid flow, acceleration, wind flow, light. All this can be done by piezoelectric devices,” Priya said.
These sensors don’t need electricity to run, and can generate the power required to transmit data by harvesting mechanical energy from routine movements in the environment — footsteps, for example.
These properties, along with a relatively simple manufacturing process, have led to the ubiquitous use of piezoelectric materials in an array of devices, from speakers to touch-activated light switches to robots for medical applications.
The greater the mechanical input, or stress, on a piezoelectric material, the larger the voltage it generates. Some materials are more sensitive than others, generating larger voltages from the same amount of stress; these make the most precise sensors.
To achieve huge gains in sensitivity for their piezoelectric material, Priya and his coworkers targeted its texture.
Ceramic piezoelectric materials, including the lead titanate used in Priya's study, are made up of grains, similar to the bricks in a wall, that give the material a three-dimensional texture. The orientation of the grains helps determines how well the material converts mechanical stress into electricity.
In most piezoelectric materials, these grains are randomly aligned. To create a ceramic with a more organized texture, the team added a small percentage of “seed” crystals that acted like a template, allowing the grains to form and grow with similar orientations.
Thanks to the seed crystals and other additives that modified the material’s electromechanical behavior, the new material is more than three times as sensitive to mechanical input compared to other piezoelectric ceramics.
These additions can be easily incorporated into the standard procedures that are already used to manufacture these materials industrially.
“That’s the beauty of this research: we didn’t have to change what people are already using,” said Priya. “We used exactly the same machine, the same process, the same chemicals — all we do is mix this small seed crystal in the powder. But the end result is that 99 percent or more of the grains are aligned. And that gives you a 300 to 500 percent improvement in properties.”
The material is also stable at high temperatures, making it useful for automotive or aerospace applications.
Companies are already working with Virginia Tech to apply the texturing technique in their manufacturing facilities.
“We are hoping that this manufacturing process can offer U.S. companies a way to capture some new markets and design some really competitive devices,” Priya said.
Priya’s group has also developed lead-free piezoelectric ceramics, which could reduce the environmental impact of these materials.