First home built in FutureHAUS style earns design award
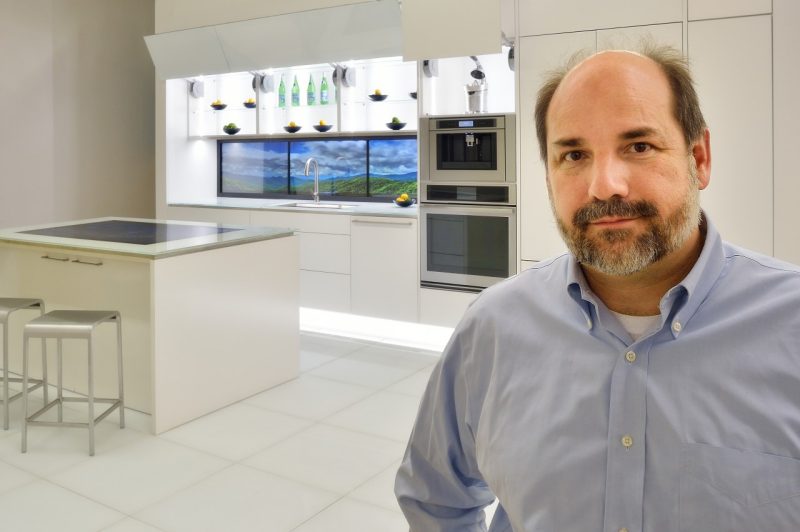
While Virginia Tech’s FutureHAUS research shows the world a revolutionary concept for the smart, modular home of the future, its creators have taken it one step further: a test in the real-world market that demonstrates its advantages over conventional construction.
Over the summer, FutureHAUS team leader Professor Joseph Wheeler and College of Architecture and Urban Studies' School of Architecture + Design alumnus Joshua Batman joined forces to construct the first residential prototype of the FutureHAUS near Charlottesville, Virginia. They were assisted by Brandon Lingenfelser, a master’s student in architecture from Blacksburg, and Ryan Alkire, a fifth-year architecture student from Mechanicsville, Virginia.
The result is LakeHAUS, a sleek, modern 2,200-square-foot home with three bedrooms, two baths, flowing open spaces, abundant natural light, and natural wood walls and floors.
The home is an architectural showpiece with one inconspicuous anomaly: It was pre-fabricated, pre-wired, and pre-finished in a warehouse, then delivered in 12 cartridges and assembled on site in a fraction of the time and labor required for typical home construction.
The house was built and sold last summer at a competitive market price to a pair of Virginia real estate agents and is the recipient of a 2016 AIA Virginia “Excellence in Architecture” Design Award presented this month in Richmond.
"With this AIA recognition, we are able to demonstrate to the public that the prefab process can not only deliver smart construction, but good design as well,” Wheeler said. “This home is tangible proof that traditional methods of stick-built, on-site home construction are on their way out. Prefabricated home components are the inevitable wave of the future, particularly with the added demands to integrate modern technologies.”
Virginia Tech’s FutureHAUS team has earned worldwide recognition for their modular building system, in which home components, such as bathrooms, kitchens, and audiovisual walls, are made in a factory. The process allows all electrical, plumbing, and digital technologies to be integrated, installed, and tested in a controlled environment before being transported in cartridges to the building site. It also simplifies the construction process by eliminating complex coordination of tradesmen on site, reducing construction time and costs, and improving quality, sustainability, and safety practices.
The LakeHAUS home is as a project of Hauscraft, a business partnership between Wheeler and his former student, Batman, an architect in Charlottesville, and his sister, Natalie Batman, the company’s director of operations. Their aim is to craft homes that integrate design and construction to create cutting-edge, sustainable spaces that complement the inhabitants, community, and the natural environment.
Wheeler’s FutureHAUS research recently earned him a spot among the nation’s top 100 most-innovative people in housing from Hanley Wood’s Builder magazine. His HIVE 100 Innovators Award placed him with prominent awardees, including Tesla CEO Elon Musk.
Last month, the FutureHAUS team helped design the concept home of the future at the International Greenbuild Conference in Los Angeles. A partnership between KB Home, Virginia Tech, KGTY Architecture + Planning, and Hanley Wood, the home modeled how cartridge technology can be the wave of the future for high-production home builders.
“We’re excited to see the housing industry approaching Virginia Tech and embracing the FutureHAUS concept as the way to a more sustainable, efficient future for housing,” Wheeler said. “Given the dire projections for worsening global population, housing, and environmental conditions over the next several decades, we believe the FutureHAUS model is the most reasonable antidote for the industry."