Wooden structures prefabricated in the U.S. could help reduce housing deficit in Latin America
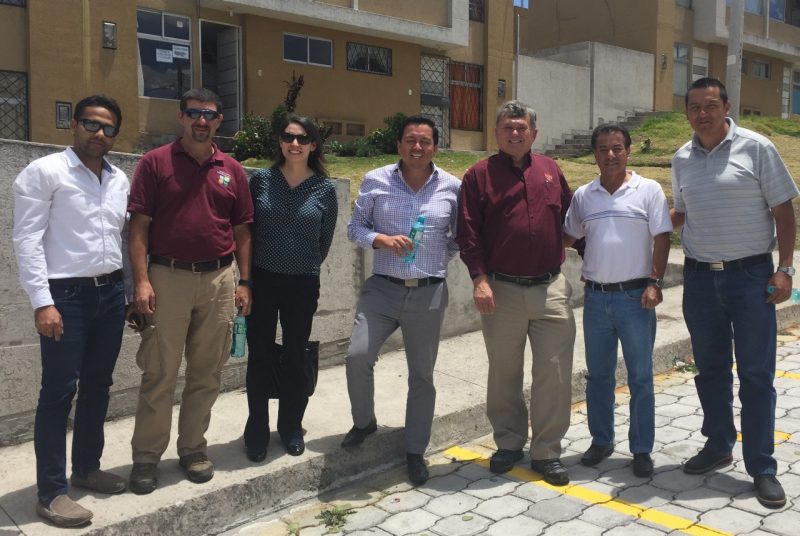
The United Nations Human Settlements Programme estimates that, if left unchecked, the worldwide slum population will reach 3 billion by the year 2050.
That’s why researchers in Virginia Tech’s College of Natural Resources and Environment are investigating the market potential for wooden houses prefabricated in the U.S. as a way to help decrease the housing deficit in Latin America.
The research team from the Department of Sustainable Biomaterials traveled to Peru, Ecuador, and Colombia to determine the market for using wood in residential and commercial structures as well as the barriers that prevent the use of wood in social housing projects.
The current housing deficit in Central and South America is more than 42 million units; Peru, Ecuador, and Colombia have deficit rates of 78 percent, 50 percent, and 32 percent, respectively.
According to research team leader Henry Quesada, associate professor of wood science and a Virginia Cooperative Extension specialist, the main factors driving the housing deficit in these countries are lack of both funding and appropriate government policies.
“There is currently a progressive agenda in countries such as Ecuador, Columbia, and Peru. At the industry and government level, stakeholders are coming together to decrease this housing deficit,” Quesada said.
“There is also a substantial agreement among stakeholders in those countries to design and build more affordable housing solutions that use renewable materials, increase energy efficiency, and, in general, have low environmental impact,” he continued.
Gaurav Kakkar, of Punjab, India, a master’s degree student in sustainable biomaterials working on the project, added, “During our meetings with government officials, local construction industry representatives, and university research centers, we found that there is little knowledge of the use of renewable materials and better construction practices.
“All of the social housing projects we visited use concrete and steel as the main construction materials,” Kakkar continued. “Wood is not an alternative right now in the countries we visited because there is little to no sustainable supply. In addition, architects and civil engineers there do not have the technical background to design wood structures, specifically for high-rise buildings in urban settings.”
After taking both environmental impact and cost into account, the researchers believe they have found a promising solution: prefabricated wooden homes.
These structures, which could be manufactured in the U.S. to specific international standards, packed in containers, and exported around the world, would provide affordable housing with low environmental impact and ease of construction.
“There are many wooden prefabricated home manufacturers on the East Coast that have extensive expertise in developing these kind of solutions,” Quesada said. “Our research team is working with one of them to help improve their logistics export operations.”
Robert “Bob” Smith, professor of forest products marketing and head of the Department of Sustainable Biomaterials, pointed out, “The southeastern U.S. along with the Appalachian region is considered the country’s wood basket. Currently, more timber is grown in the U.S. than is harvested, which has been an important driver to increase exports of the wood products. U.S. exports of logs, lumber, wood composites, and other wood products totaled $9.7 billion in fiscal year 2014, but only a small portion of that corresponds to higher-value products, such as prefabricated wooden buildings.
“The opportunity to increase the export of higher-value products, such as prefabricated homes, could mean an increase in economic development for the industry and specifically for rural areas in the southeastern and Appalachian regions where many jobs depend on the forest industry,” continued Smith, who is co-principal investigator on the project.
The research team agrees that one of the biggest challenges is the cultural acceptance of wood as a construction material. In general, people in the countries they visited perceive that wood is not as resistant to fire, earthquakes, or decay as concrete or steel.
After an earthquake hit the coast of Ecuador in early 2016, however, that perception is changing in favor of wooden structures.
“After the terrible tragedy in Ecuador, residents witnessed that most of the structures that remained standing were made of wood or bamboo,” Quesada said.
Kakkar added, “Our initial findings indicate that there is an opportunity to export prefabricated wooden homes manufactured in the U.S. to Latin America — not just because of their affordability, aesthetic beauty, ease of construction, and resistance to natural phenomena, such as earthquakes, but also because of the focus on using renewable materials and their low environmental impact.”
The data collected during these visits will be used to develop a marketing handbook for manufacturers in the U.S. looking to export prefabricated wooden homes. The handbook will include not only the marketing aspects but also logistics issues related to the packaging, transportation, and installation of the structures.
The team’s work has been supported through a competitive research grant from the U.S Department of Agriculture’s Federal State Marketing Improvement Program.