Industry partnerships fuel packaging lab improvements that enhance student learning
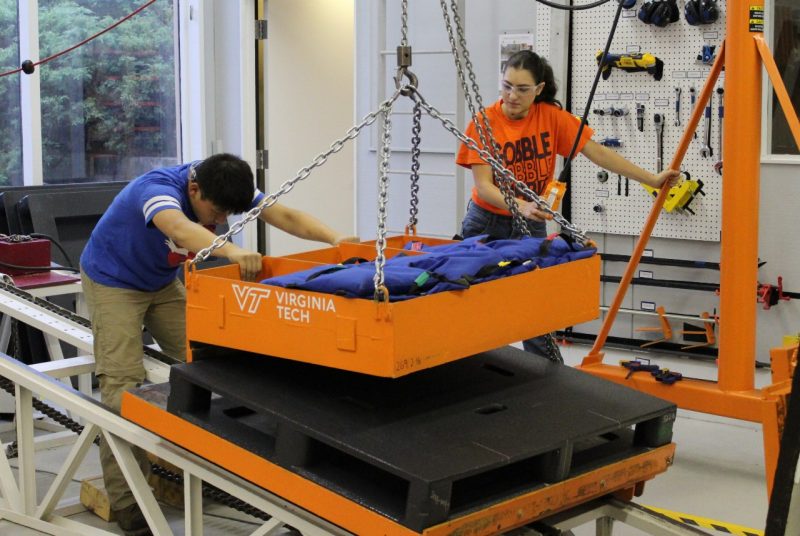
Often, the best way to learn something new is to give it a try.
Virginia Tech’s Center for Packaging and Unit Load Design offers a unique, hands-on experience in which students learn to use equipment and procedures that will be vital to their success in the packaging industry.
Now, partnerships with several firms have opened the door for additional learning opportunities as well as improvements to the packaging systems and design undergraduate degree program and to the center’s research and testing laboratories, based in the College of Natural Resources and Environment’s Department of Sustainable Biomaterials.
Lightning Technologies and GARD Pallet, both known for the innovative Lightning-GARD pallet, jointly donated $50,000 to purchase a range of sensors for use in the lab. According to Laszlo Horvath, associate professor and director of the Center for Packaging and Unit Load Design, the sensors have the potential to radically change how global packaging and distribution work — and give Virginia Tech students an edge in the industry.
Each sensor measures something different, from changes in temperature and relative humidity to the vibration and shock absorbed by a truck as it moves down the highway, enabling companies to gather information about how their products are being shipped and distributed and make cost-saving decisions based on that data.
“For example, many foods and medicines go bad quickly if they aren’t kept at a certain temperature,” Horvath said. “If temperature sensors are installed in the trucks that carry these shipments, the company will be notified as soon as the temperature changes so the truck driver can be alerted that something is wrong.”
According to Horvath, students will learn to use the sensors to collect and analyze data, as well as identify which sensors will be most useful in various scenarios. This fall, students will partner with American Woodmark, a Virginia-based furniture manufacturer, to place sensors in some of their shipments. The students will collect vibration data while the shipments are in transit and explore what happens if issues arise at any point within the company’s material handling system.
“Distribution packaging isn’t currently an area where we use a lot of high-tech sensors, but we want to build a program around smart and connected packaging,” Horvath said. “We’re developing a cutting-edge program that is at the intersection of business and science, and will help prepare students to make decisions regarding this technology that will benefit their employers.”
Industry leaders agree that Virginia Tech students are learning how to utilize technology and provide research and data that will lead to significant improvements in the industry in the years ahead.
“I have been in the pallet industry for more than 25 years and am most excited by the technology and innovation we have accomplished with the Lightning-GARD pallet,” said Rex Lowe, founder and CEO of GARD Pallet in Dallas, Texas, which sells and leases the Lightning-GARD pallet to industry clients. “It is my pleasure for GARD to support the Center for Packaging and Unit Load Design as it looks for further ways to enhance the pallet industry that, before the Lightning-GARD pallet, hadn’t changed to any large degree in the past nearly 100 years.”
Jeffrey Owen, founder and CEO of Lightning Technologies Inc. in Oxford, Michigan, added, “The research conducted by Virginia Tech’s Center for Packaging and Unit Load Design is extremely important to the pallet industry and supply chain. We are so pleased to support its ongoing work for the industry, as well as in teaching the students of today and tomorrow to become our next generation of professional engineers and researchers. All of us at Lightning Technologies have a high regard for Dr. Horvath and his team.”
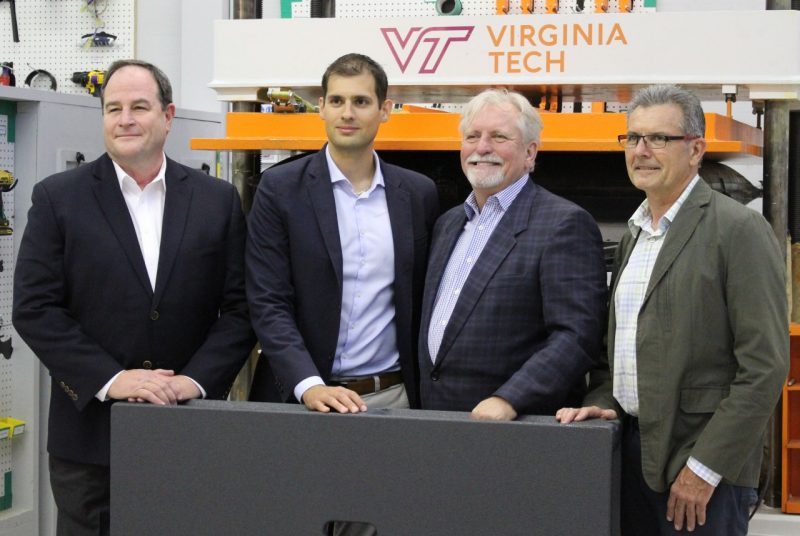
This latest development is part of a five-year-long effort to complete a lean management transformation in the center’s laboratories, in which Horvath and his students rely on the 5S process: sort, set in order, shine, standardize, and sustain. They began by removing unnecessary items from the lab, reorganizing equipment, and developing a standardized cleaning and equipment replenishment system.
Last year, Grupo Phoenix, an international packaging company, made a $50,000 donation to help complete the process and give students a chance to master lean management concepts before they enter the workforce.
“Lean management is centered around the idea of continuous improvement,” Horvath said. “We’re always looking for ways to improve the testing process for materials while reducing waste.”
The donation provided funds to install a new floor, paint the walls and color-code equipment, and install peg boards to ensure tools remain visible and organized. So far, the students have changed the way tools and equipment are stored, and how items in the lab are labeled. They are currently conducting 5S improvements to the storage space and wood shop. The students also use GoPro cameras to conduct time studies with the overall goal of generating cycle times for select laboratory equipment.
Horvath explained that with the continuous improvement mentality, students learn to constantly evaluate processes and then adapt their efforts to maximize efficiency and safety.
“Lean management is about efficiency, but it’s also about safety,” he said. “When the lab becomes more lean, the hazards disappear. You have clear walkways, tools stored in their proper places, and everything becomes more easy to access.”
Horvath added that he is excited about the improvements the students have made, because in doing so, they will be better prepared to implement lean management strategies in future internships and jobs.
“A lot of companies want to make this transformation, but many don’t succeed. The system is easy to set up, but it takes effort to maintain. By having the students work on these improvements, we’re not only teaching them how to run the tests on packages and evaluate solutions, but also to think with a continuous improvement mentality. They’ll be valuable to employers because they’ll come in knowing how to identify problems and fix them.”
Media contact for Lightning Technologies: Jeff Caponigro, jcap@caponigro.com, 248-353-3270